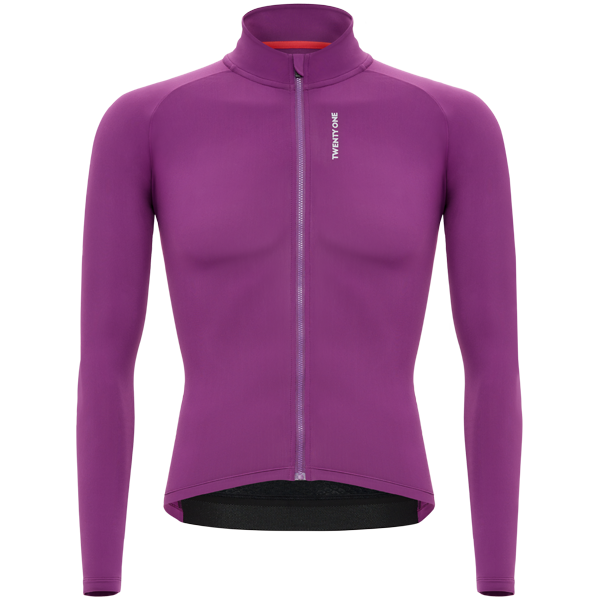
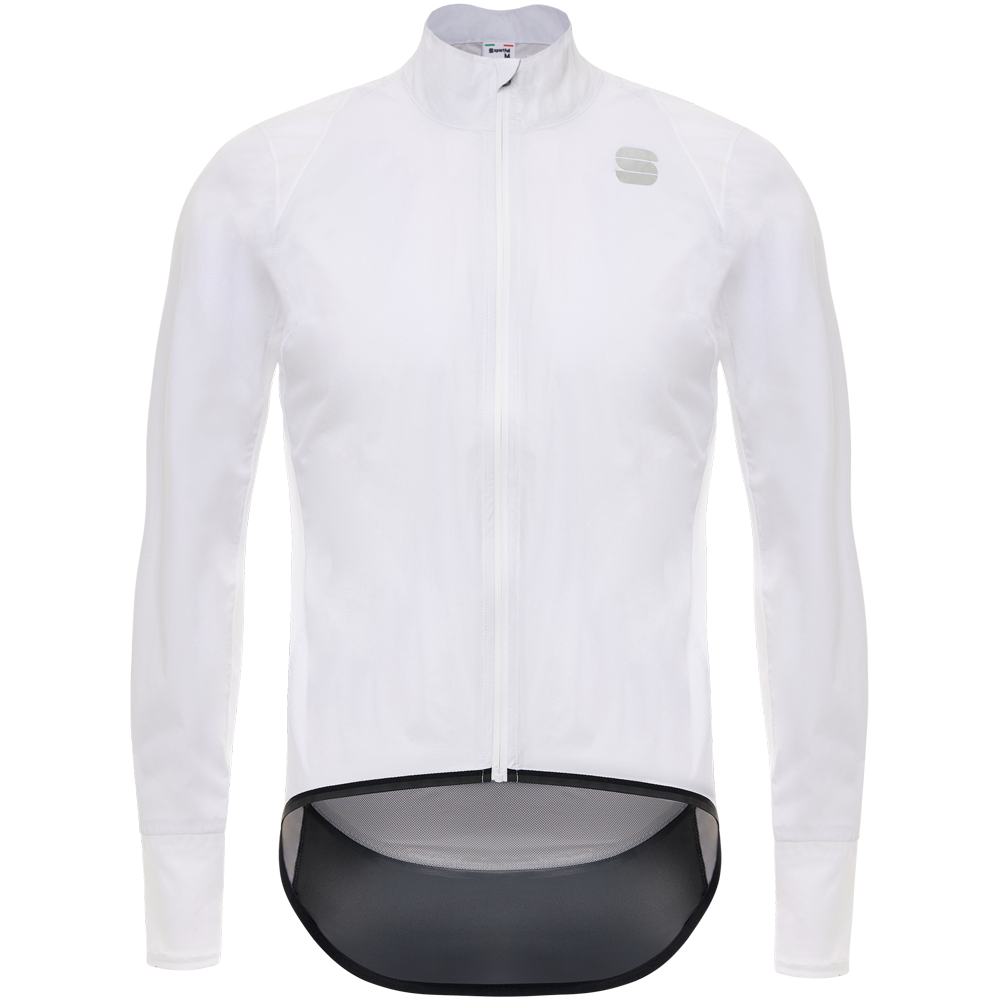
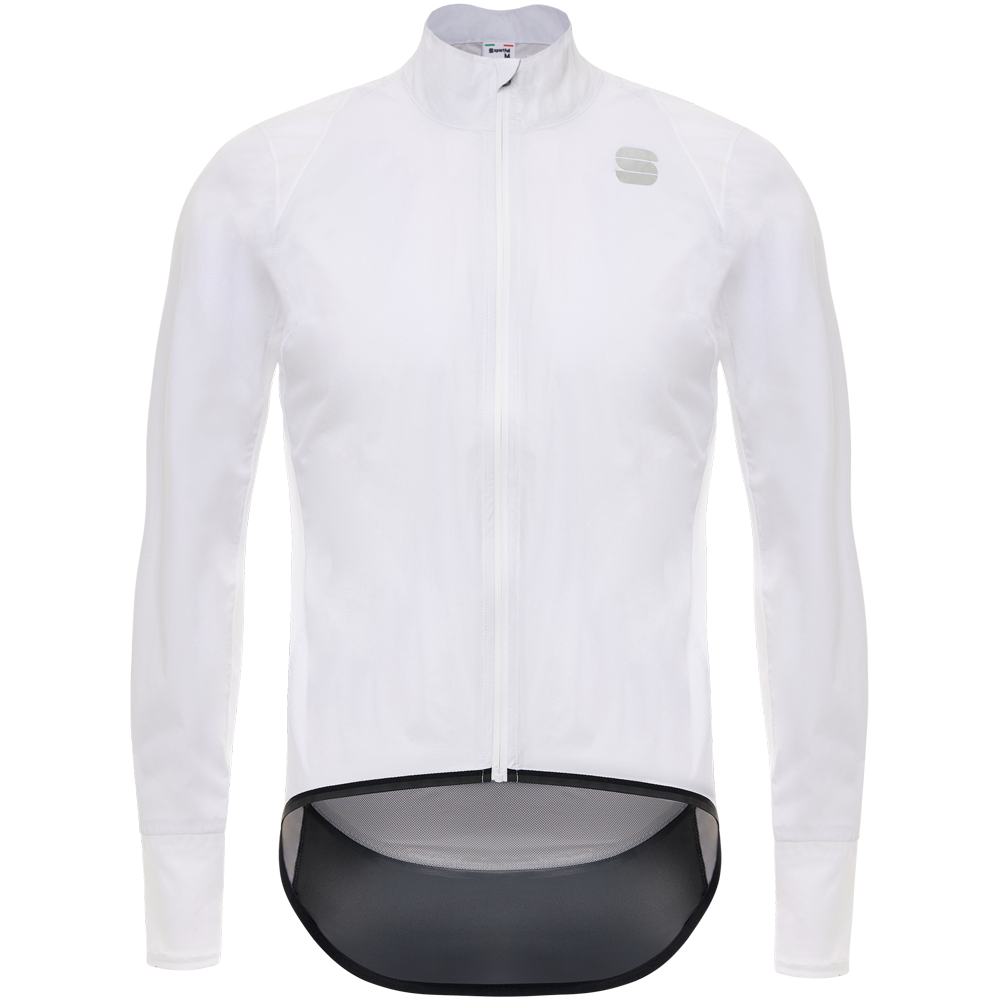
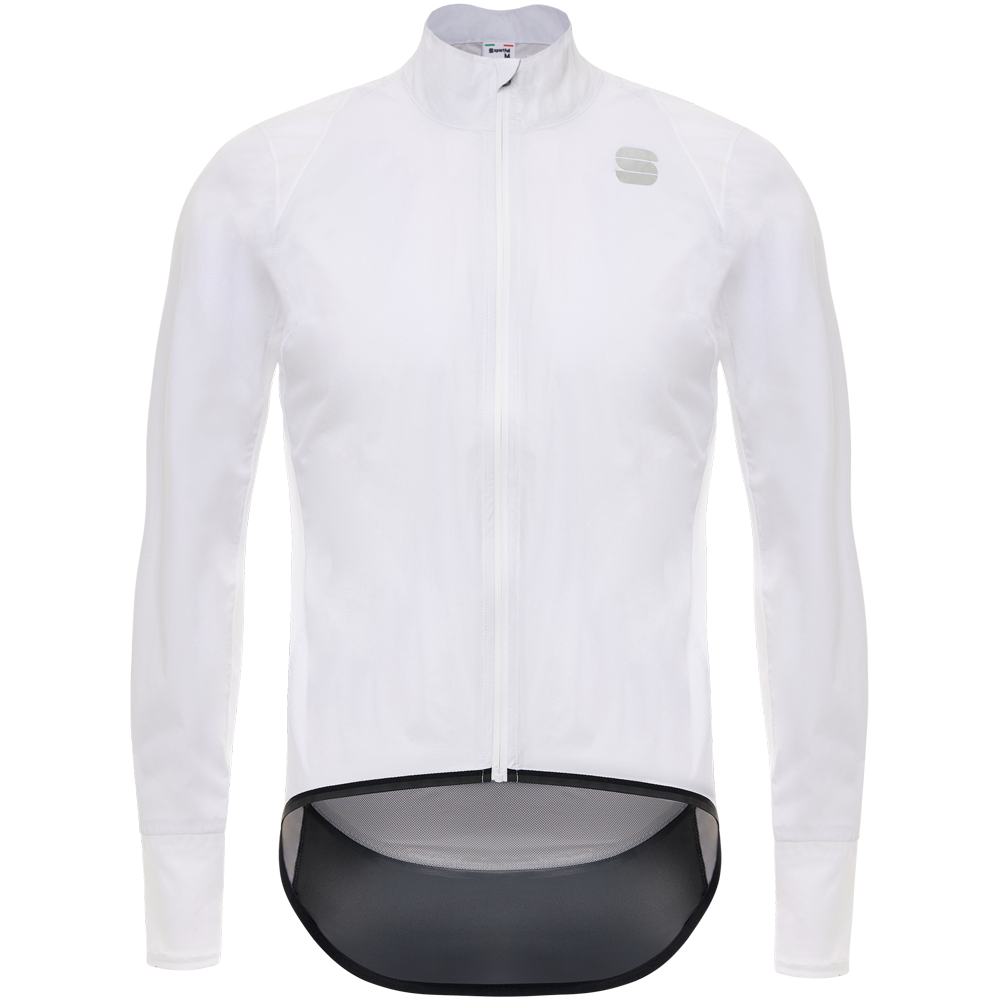
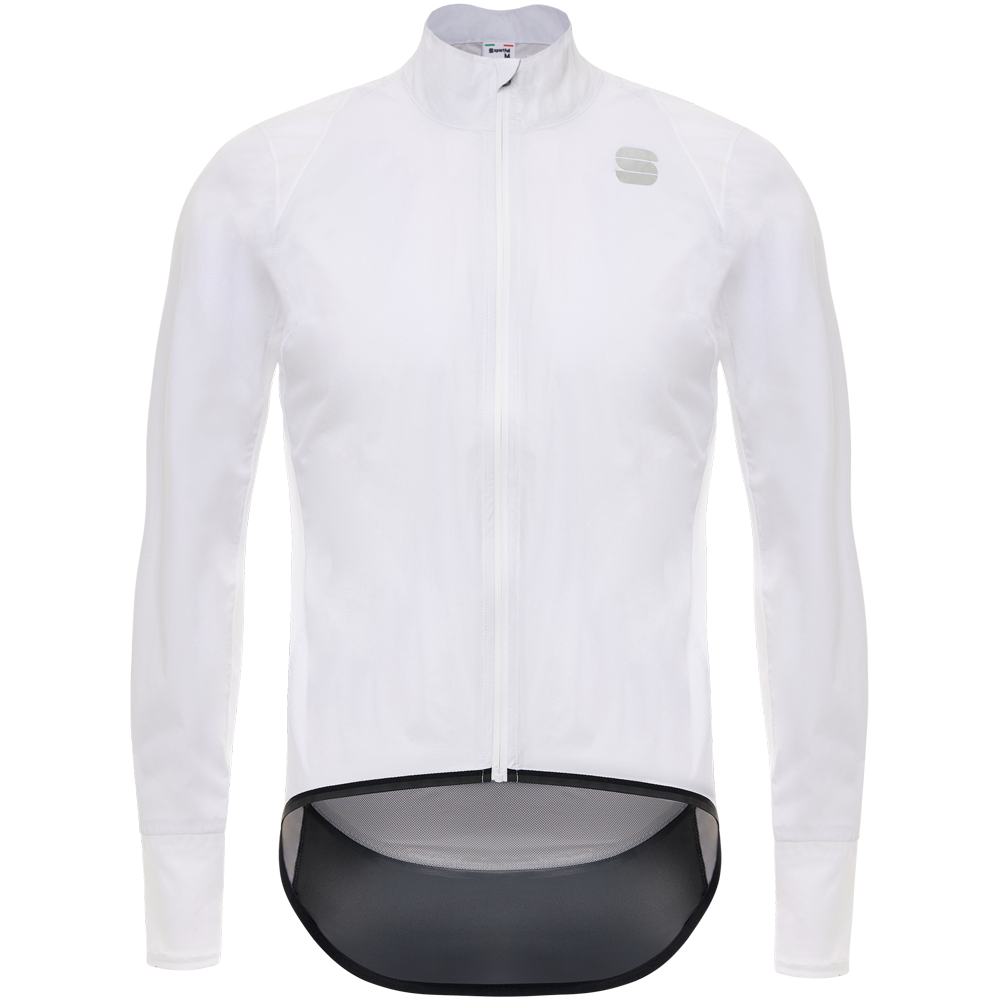
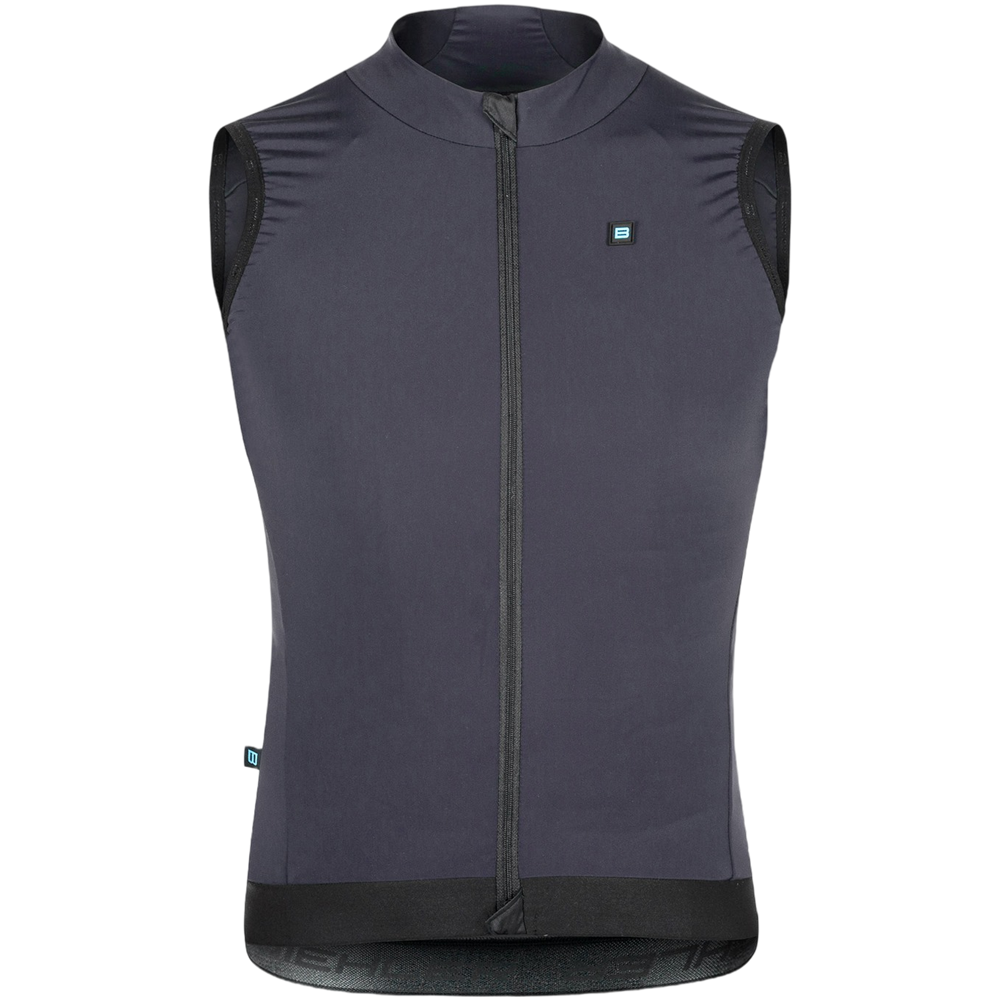
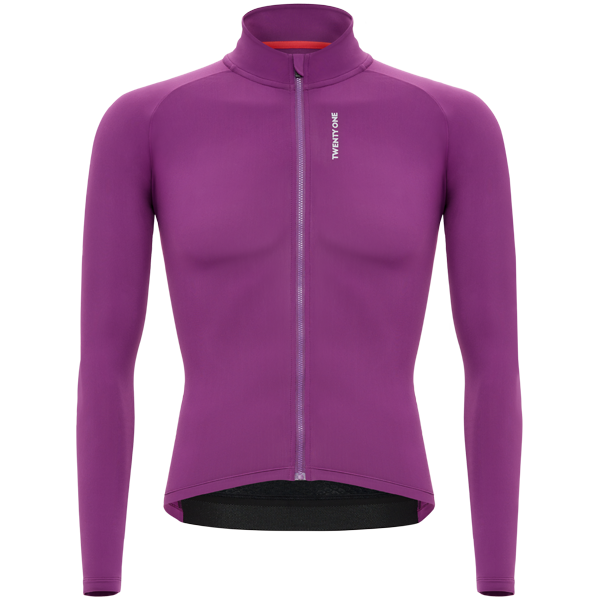
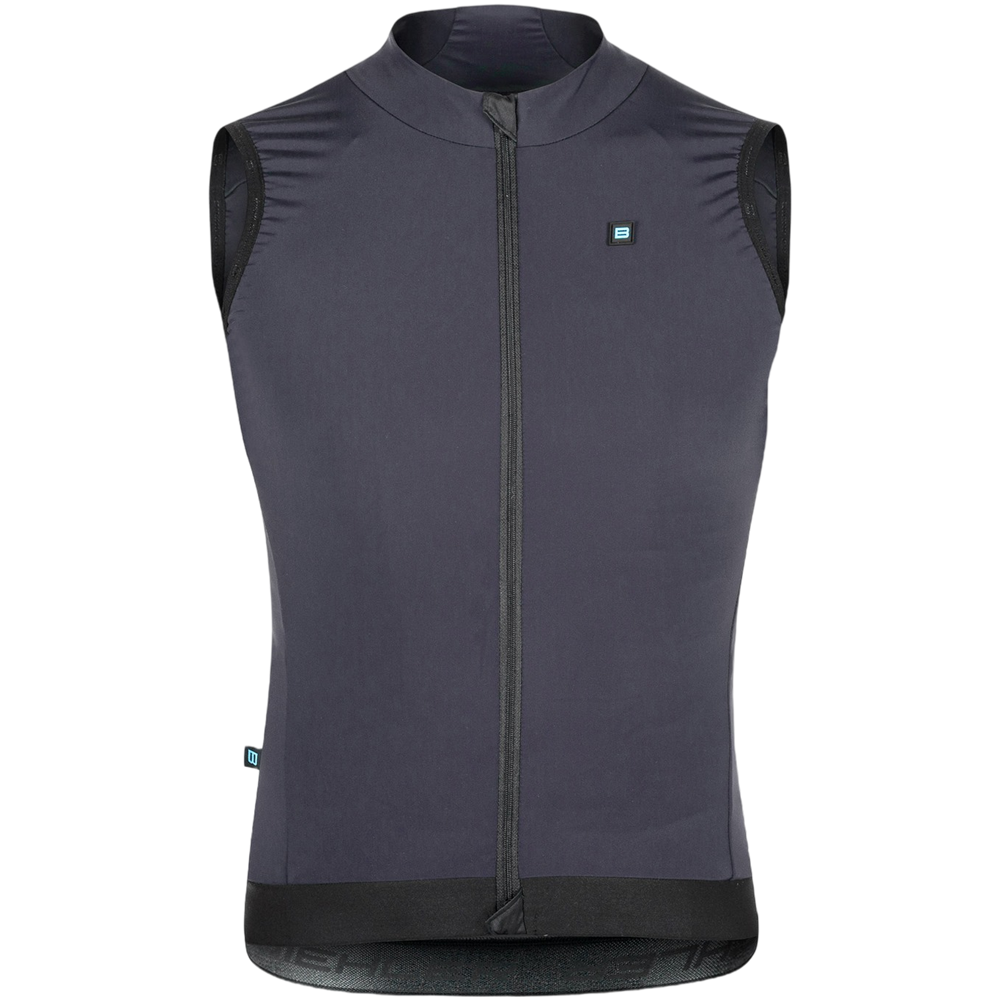
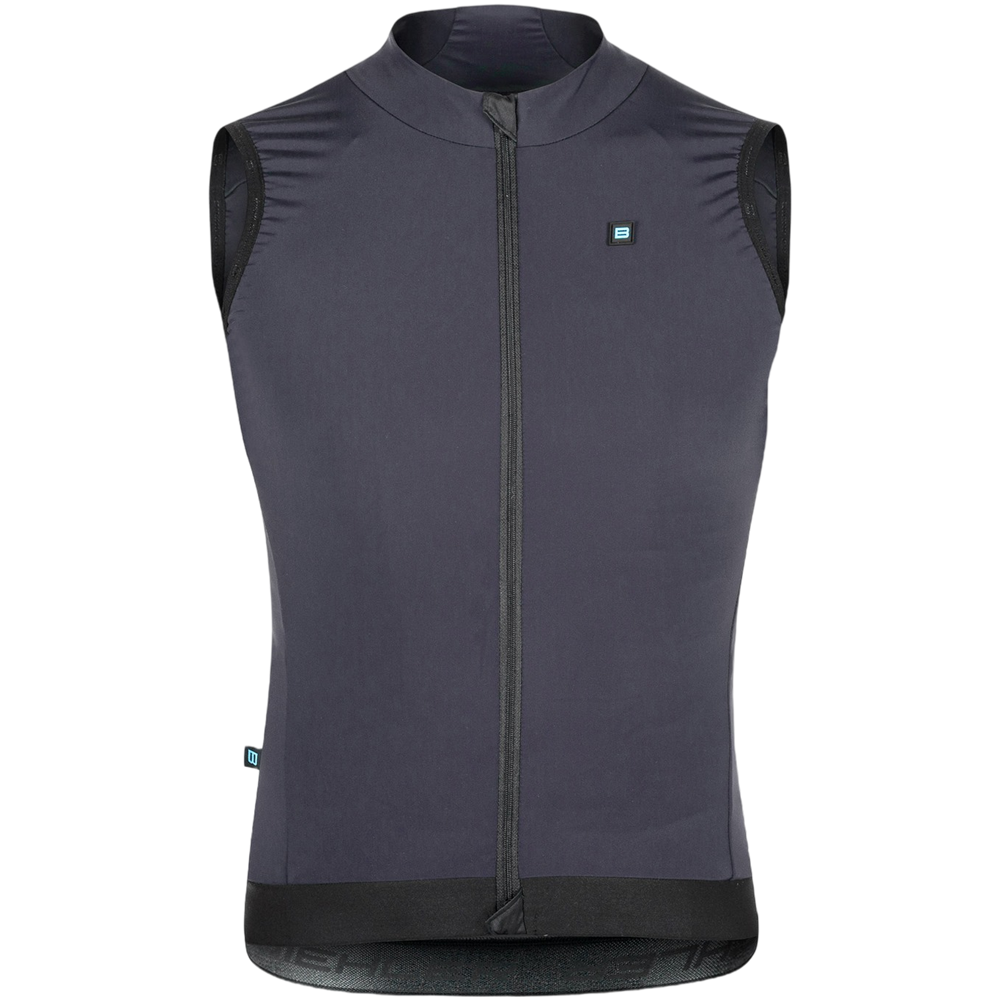
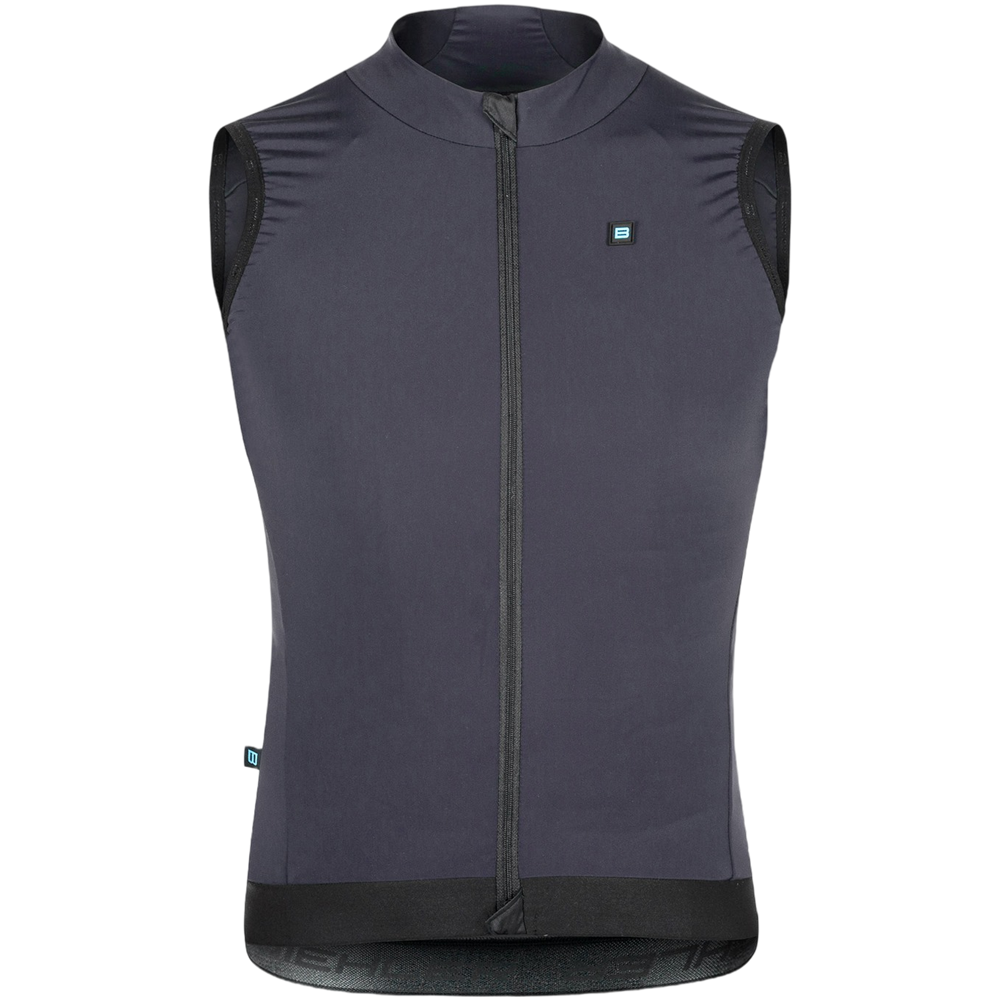
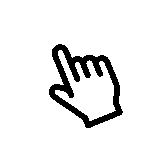
Each KASK helmet starts as a simple polycarbonate sheet, a blank (and transparent, in fact) canvas for crafting.
Each sheet undergoes a silkscreen printing process, where colors are applied using printing ink and a frame. The polycarbonate sheets are then cut to size and shape with precision cutting machines.
Each KASK helmet starts as a simple polycarbonate sheet, a blank (and transparent, in fact) canvas for crafting.
Each sheet undergoes a silkscreen printing process, where colors are applied using printing ink and a frame. The polycarbonate sheets are then cut to size and shape with precision cutting machines.
Each KASK helmet starts as a simple polycarbonate sheet, a blank (and transparent, in fact) canvas for crafting.
Each sheet undergoes a silkscreen printing process, where colors are applied using printing ink and a frame. The polycarbonate sheets are then cut to size and shape with precision cutting machines.
Each KASK helmet starts as a simple polycarbonate sheet, a blank (and transparent, in fact) canvas for crafting.
Each sheet undergoes a silkscreen printing process, where colors are applied using printing ink and a frame. The polycarbonate sheets are then cut to size and shape with precision cutting machines.
Each KASK helmet starts as a simple polycarbonate sheet, a blank (and transparent, in fact) canvas for crafting.
Each sheet undergoes a silkscreen printing process, where colors are applied using printing ink and a frame. The polycarbonate sheets are then cut to size and shape with precision cutting machines.
Each KASK helmet starts as a simple polycarbonate sheet, a blank (and transparent, in fact) canvas for crafting.
Each sheet undergoes a silkscreen printing process, where colors are applied using printing ink and a frame. The polycarbonate sheets are then cut to size and shape with precision cutting machines.
Each KASK helmet starts as a simple polycarbonate sheet, a blank (and transparent, in fact) canvas for crafting.
Each sheet undergoes a silkscreen printing process, where colors are applied using printing ink and a frame. The polycarbonate sheets are then cut to size and shape with precision cutting machines.
Each KASK helmet starts as a simple polycarbonate sheet, a blank (and transparent, in fact) canvas for crafting.
Each sheet undergoes a silkscreen printing process, where colors are applied using printing ink and a frame. The polycarbonate sheets are then cut to size and shape with precision cutting machines.
Each KASK helmet starts as a simple polycarbonate sheet, a blank (and transparent, in fact) canvas for crafting.
Each sheet undergoes a silkscreen printing process, where colors are applied using printing ink and a frame. The polycarbonate sheets are then cut to size and shape with precision cutting machines.
Each KASK helmet starts as a simple polycarbonate sheet, a blank (and transparent, in fact) canvas for crafting.
Each sheet undergoes a silkscreen printing process, where colors are applied using printing ink and a frame. The polycarbonate sheets are then cut to size and shape with precision cutting machines.
Each KASK helmet starts as a simple polycarbonate sheet, a blank (and transparent, in fact) canvas for crafting.
Each sheet undergoes a silkscreen printing process, where colors are applied using printing ink and a frame. The polycarbonate sheets are then cut to size and shape with precision cutting machines.
Each KASK helmet starts as a simple polycarbonate sheet, a blank (and transparent, in fact) canvas for crafting.
Each sheet undergoes a silkscreen printing process, where colors are applied using printing ink and a frame. The polycarbonate sheets are then cut to size and shape with precision cutting machines.
Each KASK helmet starts as a simple polycarbonate sheet, a blank (and transparent, in fact) canvas for crafting.
Each sheet undergoes a silkscreen printing process, where colors are applied using printing ink and a frame. The polycarbonate sheets are then cut to size and shape with precision cutting machines.
Each KASK helmet starts as a simple polycarbonate sheet, a blank (and transparent, in fact) canvas for crafting.
Each sheet undergoes a silkscreen printing process, where colors are applied using printing ink and a frame. The polycarbonate sheets are then cut to size and shape with precision cutting machines.
Each KASK helmet starts as a simple polycarbonate sheet, a blank (and transparent, in fact) canvas for crafting.
Each sheet undergoes a silkscreen printing process, where colors are applied using printing ink and a frame. The polycarbonate sheets are then cut to size and shape with precision cutting machines.
Each KASK helmet starts as a simple polycarbonate sheet, a blank (and transparent, in fact) canvas for crafting.
Each sheet undergoes a silkscreen printing process, where colors are applied using printing ink and a frame. The polycarbonate sheets are then cut to size and shape with precision cutting machines.
Each KASK helmet starts as a simple polycarbonate sheet, a blank (and transparent, in fact) canvas for crafting.
Each sheet undergoes a silkscreen printing process, where colors are applied using printing ink and a frame. The polycarbonate sheets are then cut to size and shape with precision cutting machines.
Each KASK helmet starts as a simple polycarbonate sheet, a blank (and transparent, in fact) canvas for crafting.
Each sheet undergoes a silkscreen printing process, where colors are applied using printing ink and a frame. The polycarbonate sheets are then cut to size and shape with precision cutting machines.
The pre-cut polycarbonate sheets are placed into steel molds, which give the helmets their specific shape. The thermoforming machine heats and vacuum-shapes the sheet around a the mold. This creates the upper and lower shells
The pre-cut polycarbonate sheets are placed into steel molds, which give the helmets their specific shape. The thermoforming machine heats and vacuum-shapes the sheet around a the mold. This creates the upper and lower shells
The pre-cut polycarbonate sheets are placed into steel molds, which give the helmets their specific shape. The thermoforming machine heats and vacuum-shapes the sheet around a the mold. This creates the upper and lower shells
The pre-cut polycarbonate sheets are placed into steel molds, which give the helmets their specific shape. The thermoforming machine heats and vacuum-shapes the sheet around a the mold. This creates the upper and lower shells
The pre-cut polycarbonate sheets are placed into steel molds, which give the helmets their specific shape. The thermoforming machine heats and vacuum-shapes the sheet around a the mold. This creates the upper and lower shells
The pre-cut polycarbonate sheets are placed into steel molds, which give the helmets their specific shape. The thermoforming machine heats and vacuum-shapes the sheet around a the mold. This creates the upper and lower shells
The pre-cut polycarbonate sheets are placed into steel molds, which give the helmets their specific shape. The thermoforming machine heats and vacuum-shapes the sheet around a the mold. This creates the upper and lower shells
The pre-cut polycarbonate sheets are placed into steel molds, which give the helmets their specific shape. The thermoforming machine heats and vacuum-shapes the sheet around a the mold. This creates the upper and lower shells
The pre-cut polycarbonate sheets are placed into steel molds, which give the helmets their specific shape. The thermoforming machine heats and vacuum-shapes the sheet around a the mold. This creates the upper and lower shells
The pre-cut polycarbonate sheets are placed into steel molds, which give the helmets their specific shape. The thermoforming machine heats and vacuum-shapes the sheet around a the mold. This creates the upper and lower shells
The pre-cut polycarbonate sheets are placed into steel molds, which give the helmets their specific shape. The thermoforming machine heats and vacuum-shapes the sheet around a the mold. This creates the upper and lower shells
The pre-cut polycarbonate sheets are placed into steel molds, which give the helmets their specific shape. The thermoforming machine heats and vacuum-shapes the sheet around a the mold. This creates the upper and lower shells
The pre-cut polycarbonate sheets are placed into steel molds, which give the helmets their specific shape. The thermoforming machine heats and vacuum-shapes the sheet around a the mold. This creates the upper and lower shells
The pre-cut polycarbonate sheets are placed into steel molds, which give the helmets their specific shape. The thermoforming machine heats and vacuum-shapes the sheet around a the mold. This creates the upper and lower shells
The pre-cut polycarbonate sheets are placed into steel molds, which give the helmets their specific shape. The thermoforming machine heats and vacuum-shapes the sheet around a the mold. This creates the upper and lower shells
The pre-cut polycarbonate sheets are placed into steel molds, which give the helmets their specific shape. The thermoforming machine heats and vacuum-shapes the sheet around a the mold. This creates the upper and lower shells
The pre-cut polycarbonate sheets are placed into steel molds, which give the helmets their specific shape. The thermoforming machine heats and vacuum-shapes the sheet around a the mold. This creates the upper and lower shells
The pre-cut polycarbonate sheets are placed into steel molds, which give the helmets their specific shape. The thermoforming machine heats and vacuum-shapes the sheet around a the mold. This creates the upper and lower shells
Expanded polystyrene (EPS) foam blocks are cut into rough shapes. These pieces are then placed into heated molds that refine their shape to match the helmet's internal contours.
Expanded polystyrene (EPS) foam blocks are cut into rough shapes. These pieces are then placed into heated molds that refine their shape to match the helmet's internal contours.
Expanded polystyrene (EPS) foam blocks are cut into rough shapes. These pieces are then placed into heated molds that refine their shape to match the helmet's internal contours.
Expanded polystyrene (EPS) foam blocks are cut into rough shapes. These pieces are then placed into heated molds that refine their shape to match the helmet's internal contours.
Expanded polystyrene (EPS) foam blocks are cut into rough shapes. These pieces are then placed into heated molds that refine their shape to match the helmet's internal contours.
Expanded polystyrene (EPS) foam blocks are cut into rough shapes. These pieces are then placed into heated molds that refine their shape to match the helmet's internal contours.
Expanded polystyrene (EPS) foam blocks are cut into rough shapes. These pieces are then placed into heated molds that refine their shape to match the helmet's internal contours.
Expanded polystyrene (EPS) foam blocks are cut into rough shapes. These pieces are then placed into heated molds that refine their shape to match the helmet's internal contours.
Expanded polystyrene (EPS) foam blocks are cut into rough shapes. These pieces are then placed into heated molds that refine their shape to match the helmet's internal contours.
Expanded polystyrene (EPS) foam blocks are cut into rough shapes. These pieces are then placed into heated molds that refine their shape to match the helmet's internal contours.
Expanded polystyrene (EPS) foam blocks are cut into rough shapes. These pieces are then placed into heated molds that refine their shape to match the helmet's internal contours.
Expanded polystyrene (EPS) foam blocks are cut into rough shapes. These pieces are then placed into heated molds that refine their shape to match the helmet's internal contours.
Expanded polystyrene (EPS) foam blocks are cut into rough shapes. These pieces are then placed into heated molds that refine their shape to match the helmet's internal contours.
Expanded polystyrene (EPS) foam blocks are cut into rough shapes. These pieces are then placed into heated molds that refine their shape to match the helmet's internal contours.
Expanded polystyrene (EPS) foam blocks are cut into rough shapes. These pieces are then placed into heated molds that refine their shape to match the helmet's internal contours.
Expanded polystyrene (EPS) foam blocks are cut into rough shapes. These pieces are then placed into heated molds that refine their shape to match the helmet's internal contours.
Expanded polystyrene (EPS) foam blocks are cut into rough shapes. These pieces are then placed into heated molds that refine their shape to match the helmet's internal contours.
Expanded polystyrene (EPS) foam blocks are cut into rough shapes. These pieces are then placed into heated molds that refine their shape to match the helmet's internal contours.
The molded outer shell and shaped EPS foam are carefully assembled together.
The molded outer shell and shaped EPS foam are carefully assembled together.
The molded outer shell and shaped EPS foam are carefully assembled together.
The molded outer shell and shaped EPS foam are carefully assembled together.
The molded outer shell and shaped EPS foam are carefully assembled together.
The molded outer shell and shaped EPS foam are carefully assembled together.
The molded outer shell and shaped EPS foam are carefully assembled together.
The molded outer shell and shaped EPS foam are carefully assembled together.
The molded outer shell and shaped EPS foam are carefully assembled together.
The molded outer shell and shaped EPS foam are carefully assembled together.
The molded outer shell and shaped EPS foam are carefully assembled together.
The molded outer shell and shaped EPS foam are carefully assembled together.
The molded outer shell and shaped EPS foam are carefully assembled together.
The molded outer shell and shaped EPS foam are carefully assembled together.
The molded outer shell and shaped EPS foam are carefully assembled together.
The molded outer shell and shaped EPS foam are carefully assembled together.
The molded outer shell and shaped EPS foam are carefully assembled together.
At that point, padding and safety systems are incorporated and the helmet receives its final touches, including the application of decals and branding.
At that point, padding and safety systems are incorporated and the helmet receives its final touches, including the application of decals and branding.
At that point, padding and safety systems are incorporated and the helmet receives its final touches, including the application of decals and branding.
At that point, padding and safety systems are incorporated and the helmet receives its final touches, including the application of decals and branding.
At that point, padding and safety systems are incorporated and the helmet receives its final touches, including the application of decals and branding.
At that point, padding and safety systems are incorporated and the helmet receives its final touches, including the application of decals and branding.
At that point, padding and safety systems are incorporated and the helmet receives its final touches, including the application of decals and branding.
At that point, padding and safety systems are incorporated and the helmet receives its final touches, including the application of decals and branding.
At that point, padding and safety systems are incorporated and the helmet receives its final touches, including the application of decals and branding.
At that point, padding and safety systems are incorporated and the helmet receives its final touches, including the application of decals and branding.
At that point, padding and safety systems are incorporated and the helmet receives its final touches, including the application of decals and branding.
At that point, padding and safety systems are incorporated and the helmet receives its final touches, including the application of decals and branding.
At that point, padding and safety systems are incorporated and the helmet receives its final touches, including the application of decals and branding.
At that point, padding and safety systems are incorporated and the helmet receives its final touches, including the application of decals and branding.
At that point, padding and safety systems are incorporated and the helmet receives its final touches, including the application of decals and branding.
At that point, padding and safety systems are incorporated and the helmet receives its final touches, including the application of decals and branding.
At that point, padding and safety systems are incorporated and the helmet receives its final touches, including the application of decals and branding.
At that point, padding and safety systems are incorporated and the helmet receives its final touches, including the application of decals and branding.
After a thorough final inspection, the helmets are securely packaged and prepared for distribution.
After a thorough final inspection, the helmets are securely packaged and prepared for distribution.
After a thorough final inspection, the helmets are securely packaged and prepared for distribution.
After a thorough final inspection, the helmets are securely packaged and prepared for distribution.
After a thorough final inspection, the helmets are securely packaged and prepared for distribution.
After a thorough final inspection, the helmets are securely packaged and prepared for distribution.
After a thorough final inspection, the helmets are securely packaged and prepared for distribution.
After a thorough final inspection, the helmets are securely packaged and prepared for distribution.
After a thorough final inspection, the helmets are securely packaged and prepared for distribution.
After a thorough final inspection, the helmets are securely packaged and prepared for distribution.
After a thorough final inspection, the helmets are securely packaged and prepared for distribution.
After a thorough final inspection, the helmets are securely packaged and prepared for distribution.
After a thorough final inspection, the helmets are securely packaged and prepared for distribution.
After a thorough final inspection, the helmets are securely packaged and prepared for distribution.
After a thorough final inspection, the helmets are securely packaged and prepared for distribution.
After a thorough final inspection, the helmets are securely packaged and prepared for distribution.
After a thorough final inspection, the helmets are securely packaged and prepared for distribution.